About Us
Learn more about CSS’s expertise in delivering custom microchip solutions.
About Custom Silicon Solutions (CSS)
- CSS develops and supplies custom microchips with an emphasis in analog, mixed-signal, high-voltage, and wireless communications.
- CSS was founded nearly 30 years ago on the principle that the most innovative circuit solutions come from the best and brightest engineers.
- In addition to building up the world’s premier IC design team, CSS also supplies high-volume semiconductor products over the entire product lifecycle.
- Located in Irvine, CA in a state-of-the-art 30,000 sq. foot building, CSS is a one-stop-shop for all your custom ASIC needs.
About our Turnkey ASIC Expertise
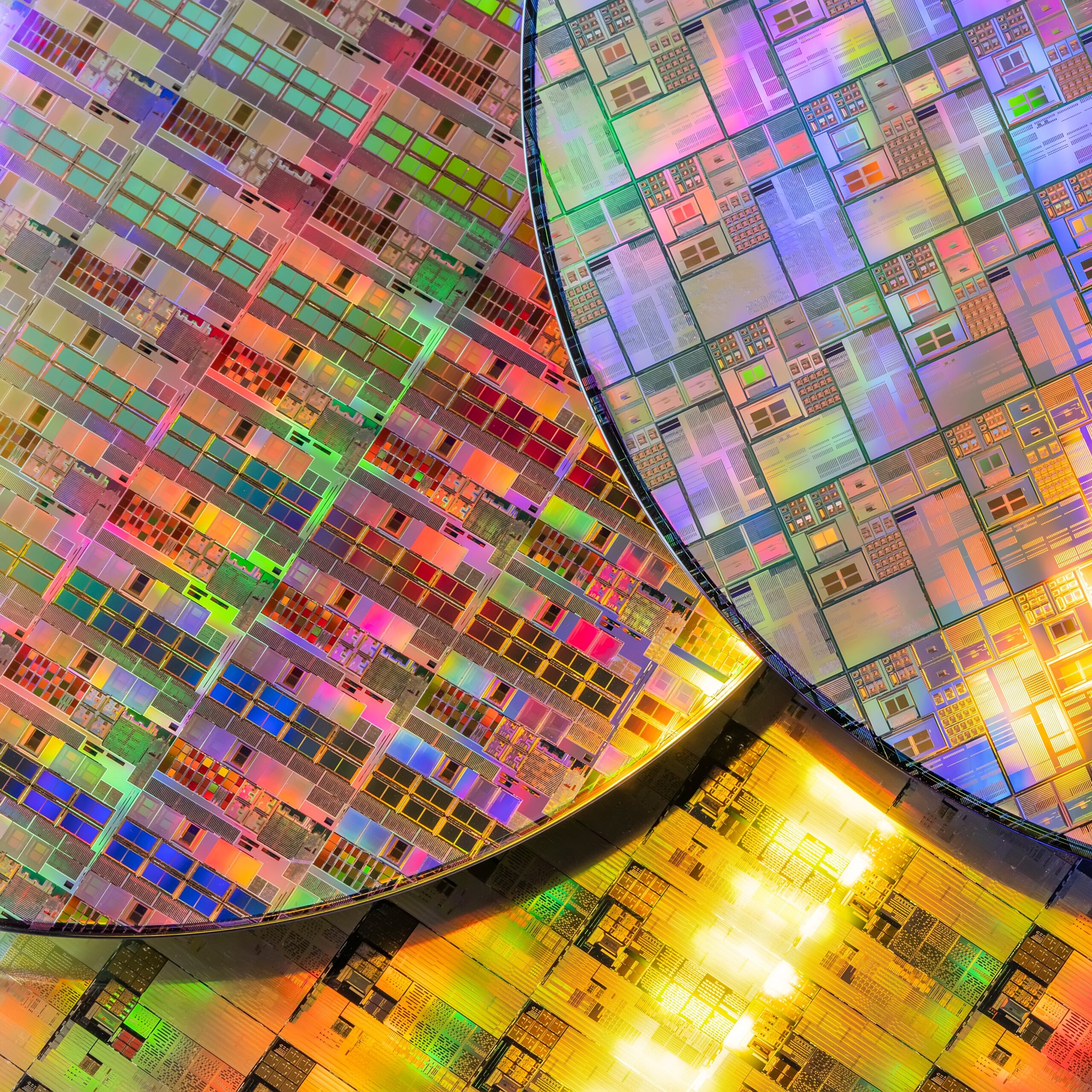
Management Team
President and CEO
John Cheng
Mr. Cheng holds a BSEE from University of California, Irvine and has 35+ years of semiconductor entrepreneurial business experience. John has led teams taping out over 300 ASIC designs in all of the major foundries using a wide variety of process nodes to service client applications in Industrial, Medical, Aerospace & Defense, and Consumer end markets. He has built up and managed engineering teams that specialize in mixed-signal SOCs, high-voltage ICs, CMOS Image Sensors, and RF designs.
Throughout his 35-year career, John has developed innovative custom integrated circuits and manufacturing services that have enabled customers to become leaders in their markets. For John, the true rewards of his entrepreneurial career come by transferring a CSS ASIC into mass production and watching it play a key role in helping a client’s business flourish.
John is also an active pilot with multiengine commercial rating, a former professional ski instructor, and a lifetime avid skier. John also plays in a rock band at local venues and is dedicated to fund raising for the Cystic Fibrosis Foundation of Orange County.
VP of Engineering and Technology
Frank Bohac
Mr. Bohac received BSEE and MSEE degrees at Purdue University, with an emphasis in integrated circuit design and solid-state physics. After completing his studies at Purdue, Frank joined the R&D group at Hughes Aircraft Company where he worked on CCD transversal filters and correlators. After helping pioneer CMOS EEPROM technology into a practical nonvolatile memory, he joined Hughes’ microelectronics group, where he designed mixed-signal ASICs for primarily industrial and automotive applications. During his 20-year tenure at Hughes, he designed over 40 integrated circuits and was issued ten patents.
In 1996, Frank and a colleague left Hughes Aircraft to start Custom Silicon Solutions (CSS). Since then, he has designed over 50 custom ASICs for Industrial, Medical, Aerospace & Defense, and Consumer markets. His areas of expertise include: SRAM, ROM & EEPROM memory design, low-voltage/ultra low-power analog CMOS design and thermal controllers.
When not innovating circuits, Frank is an avid bicycler as it helps him clear his mind and stay active. He also enjoys woodworking and gardening.
VP of Marketing and Business Development
Jared Stevenson
Mr. Stevenson brings over 23 years of semiconductor experience in areas that span from CMOS circuit design to technical marketing to business management. Jared began his career as a mixed-signal ASIC designer at AMI Semiconductor where he quickly moved into the roles of Technical Lead managing large SoC projects and then a System Architect innovating solutions to unique customer problems using available and newly developed IP and technologies. After moving into technical and strategic marketing roles, and going back to business school, Jared led the marketing and applications team for the Mixed-Signal ASIC business unit at onsemi a Strategic Marketing Manager.
Most recently Jared was the Director of the Industrial Products Business Unit at onsemi where he drove the ideation, development, and promotion of innovative IoT products that are helping enable the fourth industrial revolution. He oversaw the entire business performance of a nearly $100M organization while focusing on revenue expansion, the opportunity funnel, gross margin improvement, and strategic product development.
Jared holds a BSEE, MSEE, and MBA from Brigham Young University. When not summiting peaks in the Rocky Mountains or even Kilimanjaro, he enjoys volunteering with local youth groups to get them into the wild to experience camping and hiking in this beautiful world we call home.
About our Ecosystem Partners
Custom Silicon Solutions has nearly three decades of experience in full turnkey ASIC design and supply. While we have our own 8,000 square foot test floor where we probe and test our products in house, we have also developed strong relationships with key manufacturing and service providers for the rest of our semiconductor supply chain needs.
Semiconductor Wafer Fabricators
CSS is a fabless semiconductor supplier and thus we are fab agnostic. This simply means we are not tied to any particular wafer manufacturer and we always choose the best fab option based on providing an optimized solution for your unique ASIC. Your priorities become our priorities and we will help perform tradeoff space analyses on dimensions of price, performance, size, and power.
FAQs
What is ASIC design?
There are several different kinds of integrated circuits, including large CPUs, GPUs, power converters, and memory chips, to name just a few. An ASIC is an Application Specific Integrated Circuit, meaning that it is a custom-designed microchip dedicated to a single application. Thus, designing an ASIC requires custom circuit design, simulation, layout, and validation. Usually an ASIC is paid for by a customer and is only sold back to that customer for their specific application.
How will an ASIC solution reduce my build of materials (BOM) count and cost?
An ASIC integrates the functionality of multiple off-the-shelf components into a single die and package. Reducing cost is usually the primary motivating factor to develop an ASIC. The savings in BOM cost will repay the upfront development cost (NRE) and provide a compelling ROI. In addition, printed circuit board (PCB) assembly and testing cost is reduced due to a smaller PCB and fewer components.
How will an ASIC improve and optimize the performance and power requirements of my system?
An ASIC is customized to the exact specification agreed upon. Consequently, unnecessary performance, functionality, and power can be eliminated from a custom solution. In addition, where higher performance or new functionality needs to be added, an ASIC can be custom designed to meet the requirements.
How will an ASIC reduce the size of my system?
The functionality of multiple components will be integrated into a single chip; thus, significant size reductions are possible with fewer total components.
How will an ASIC improve the reliability of my system?
By reducing the number of components in a system, as well as the interconnect between them, reliability increases due to fewer failure points.
How will an ASIC improve the Intellectual Property protection of my system?
Integration of your system into an ASIC will increase the barrier to reverse engineering your intellectual property by one or more orders of magnitude.
Can I afford the NRE of an ASIC?
Probably. Most ASICs are very cost effective and have attractive ROIs. CSS will optimize the chip’s performance to the engineering effort required for the complete ASIC in order to reduce costs as much as possible. Given the cost savings on the BOM, as well as the PCB materials and testing, most ASICs will break even in 12 to 18 months of full production. Contact CSS today for a free quote to see how reasonably priced a full-custom ASIC can be.
Why should I choose CSS to develop our custom ASIC?
How long does a custom IC take to design, prototype, and transfer to production?
ASIC designs range from the ultra-simple, to the ultra-complex and schedules will vary accordingly. The simplest ASICs can be designed and prototyped in as little as six months, whereas the most complex devices may take over twice that long. After characterization of the ASIC, the completion of the production test program and release to production will take another 2-4 months.
What happens if I need to change a requirement after the specification has been signed and the design has already progressed?
How long does it take to get a quote?
1-2 weeks assuming the ASIC requirements are well defined.
What level of support is needed from a customer throughout the ASIC development?
During the bulk of the design phase, a weekly meeting may be sufficient to ensure we are fully aligned. However, there are two time periods where customer support is critical. First, defining and locking down the ASIC requirements. CSS cannot design in earnest until the specification is signed by both parties; much input is needed from customers during this phase. Second, significant customer engagement is needed for their prototype evaluation. It is essential that the customer define a prototype evaluation plan and execute it in a timely manner once parts are received.
I'm not an IC expert. What do I need to know to be successful?
Can the prototyping or production schedule be expedited?
Most semiconductor manufacturers and packaging vendors are open to expedited cycle times if given sufficient notice. They normally charge a fee for such expedites which, in turn, will be passed to the customer.
What is an analog signal?
How are integrated circuits made?
Integrated circuits are made by processing a thin wafer of semiconducting material in a fabrication factory (or “fab”). Transistors, diodes, resistors, capacitors, inductors, and metal interconnecting wires can be made directly onto the wafer using photo lithography coupled with implanting, growing, depositing, or removing electrically interesting materials. The processing of a wafer usually includes scores of processing steps to build up the circuit layer by layer.
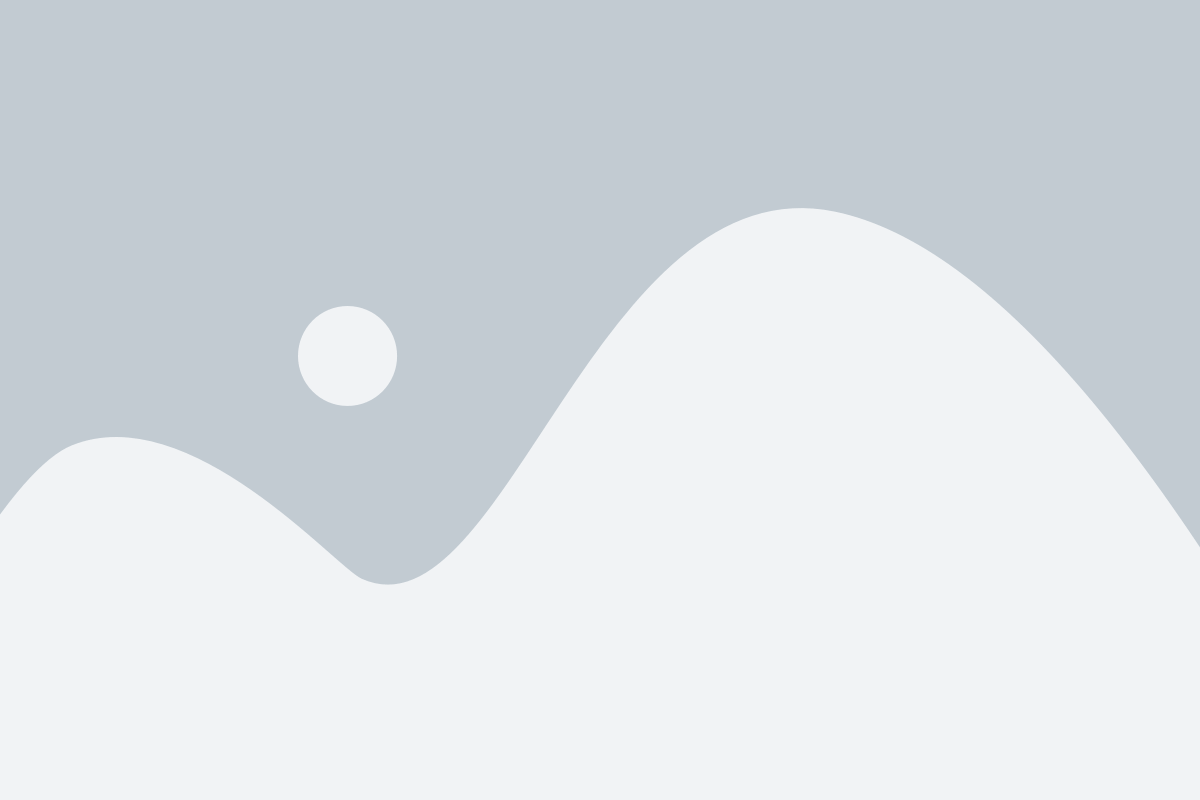
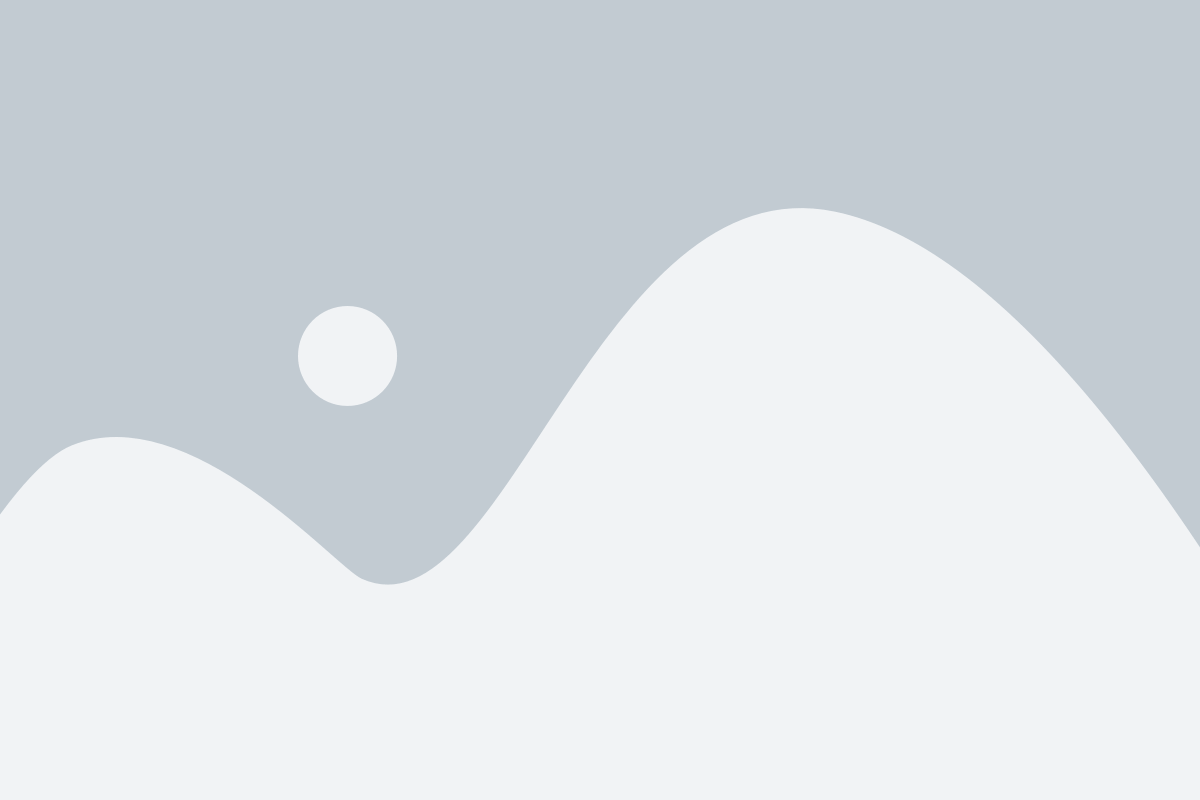
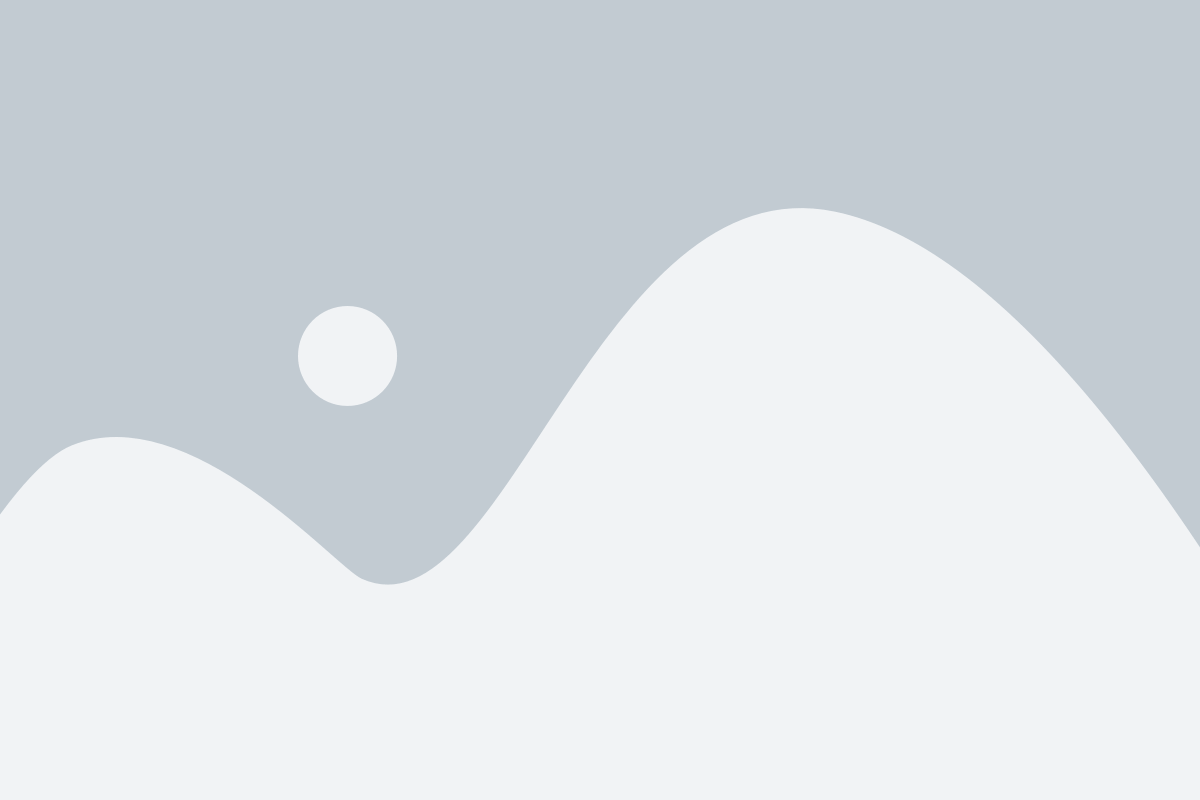